Quick model update
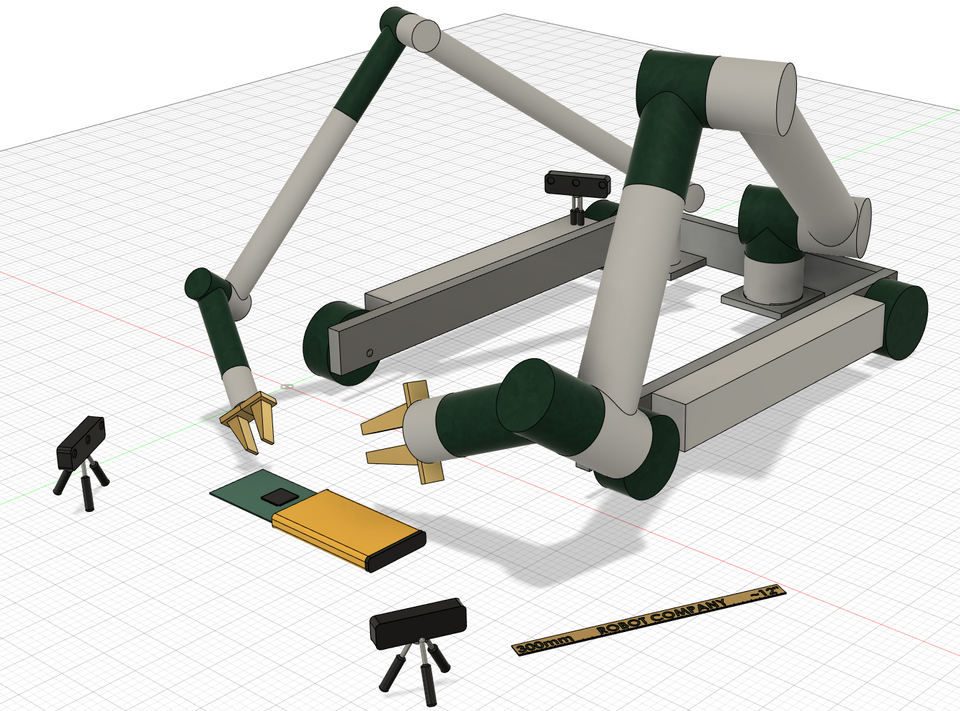
post 5
I intend to outsource some of the drawing work. In this case, it helps to have some reference shots for the artist to work from.
The first post was not quite good enough to use as a reference, and the 2nd post is missing an arm. So here is an updated model.
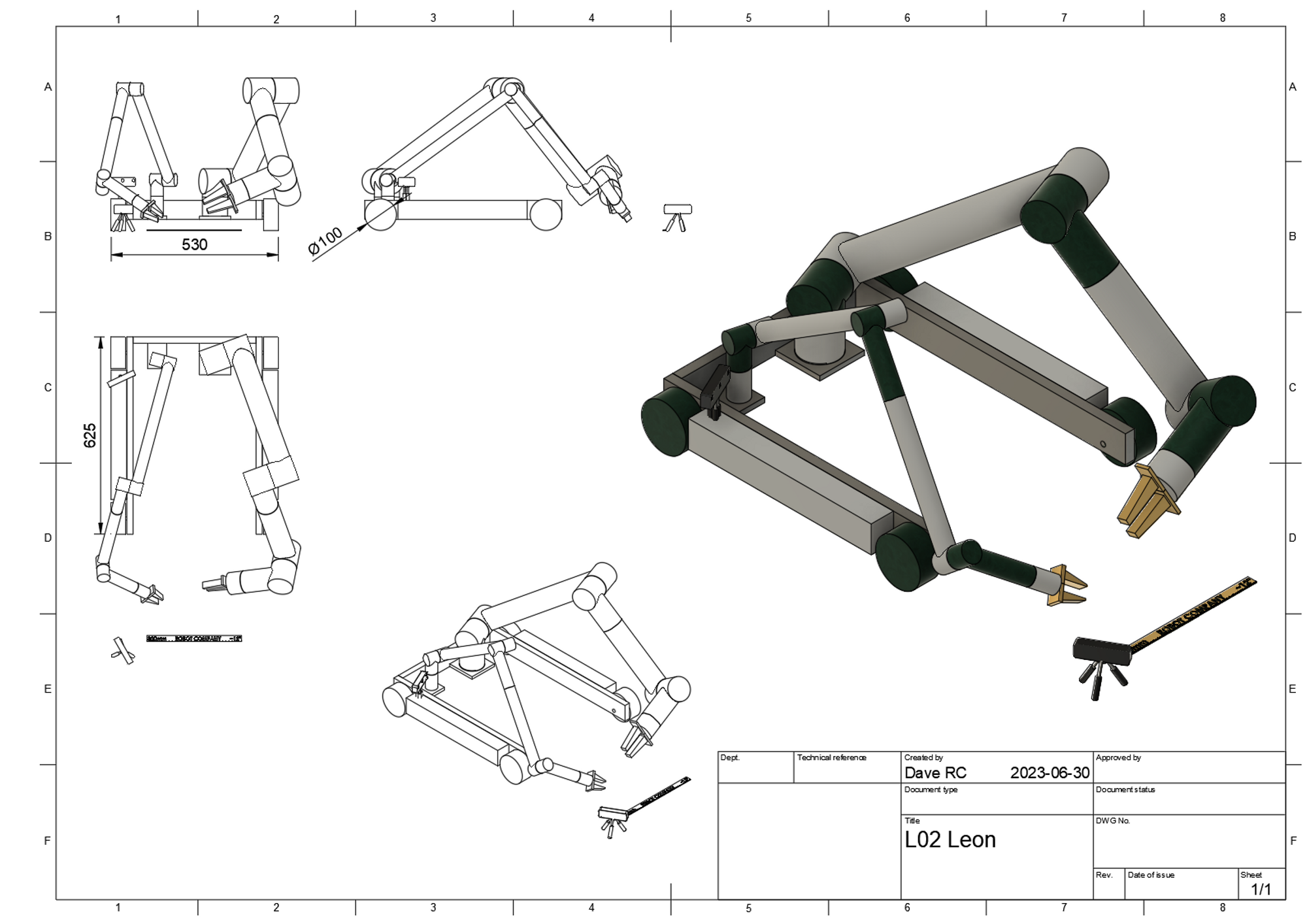
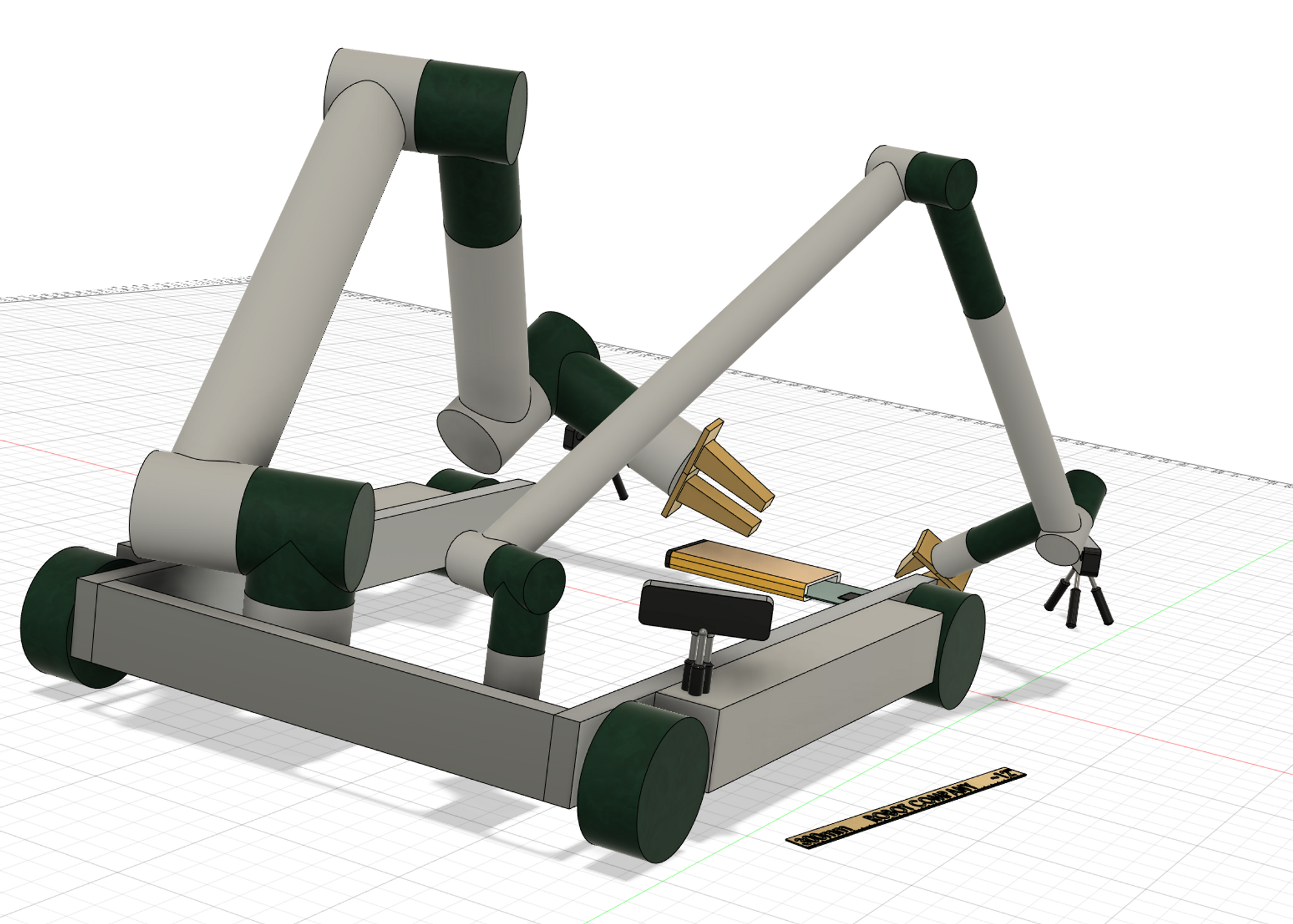
Leon's first day at work
Here I've added a job for the robot to do.
It's going to assemble this simple box by inserting the circuit board and putting the endcap on.
The box doesn't do anything.
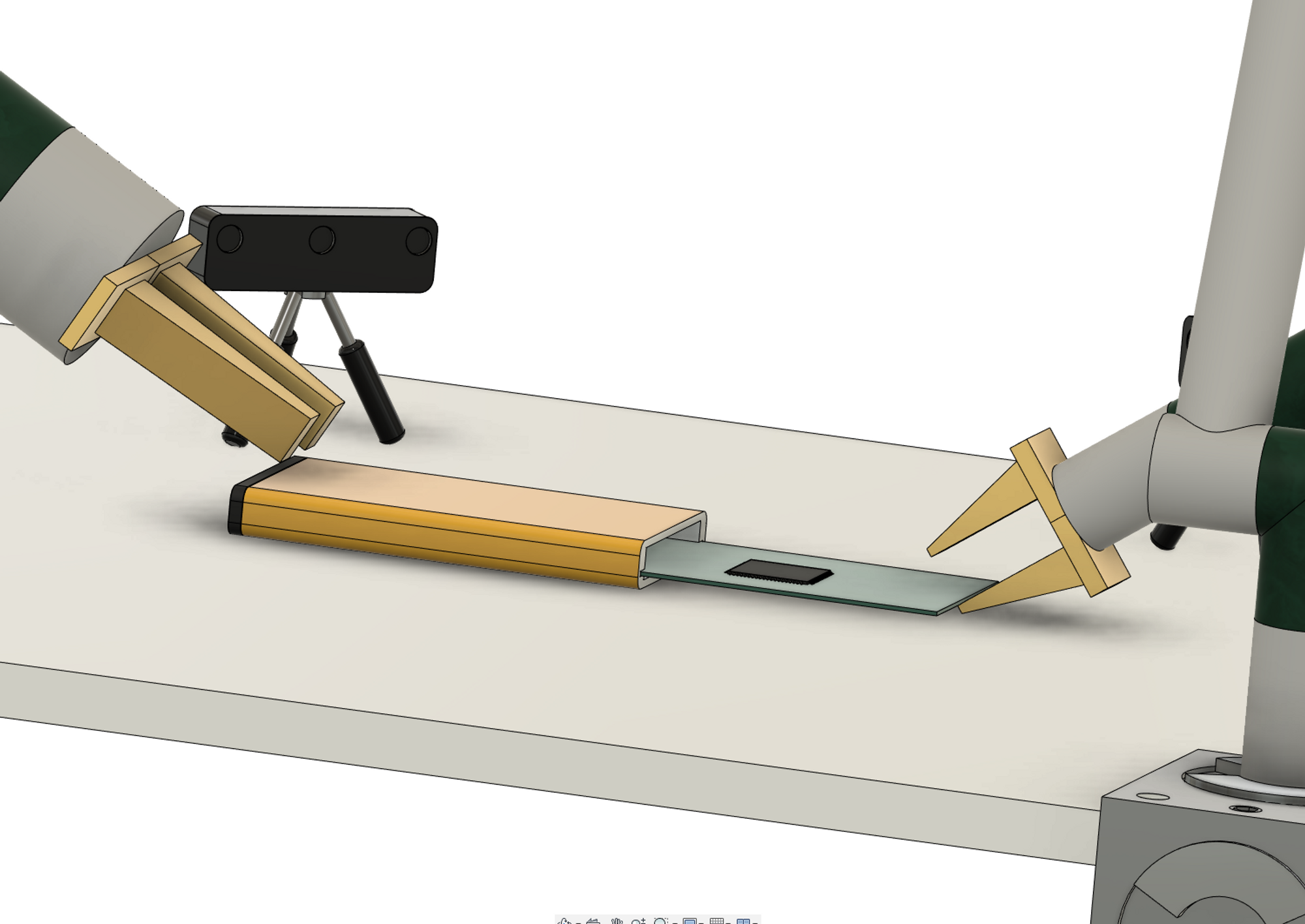
As described in Getting some height, the robot would probably work from a desk, rather than do this job on the floor.
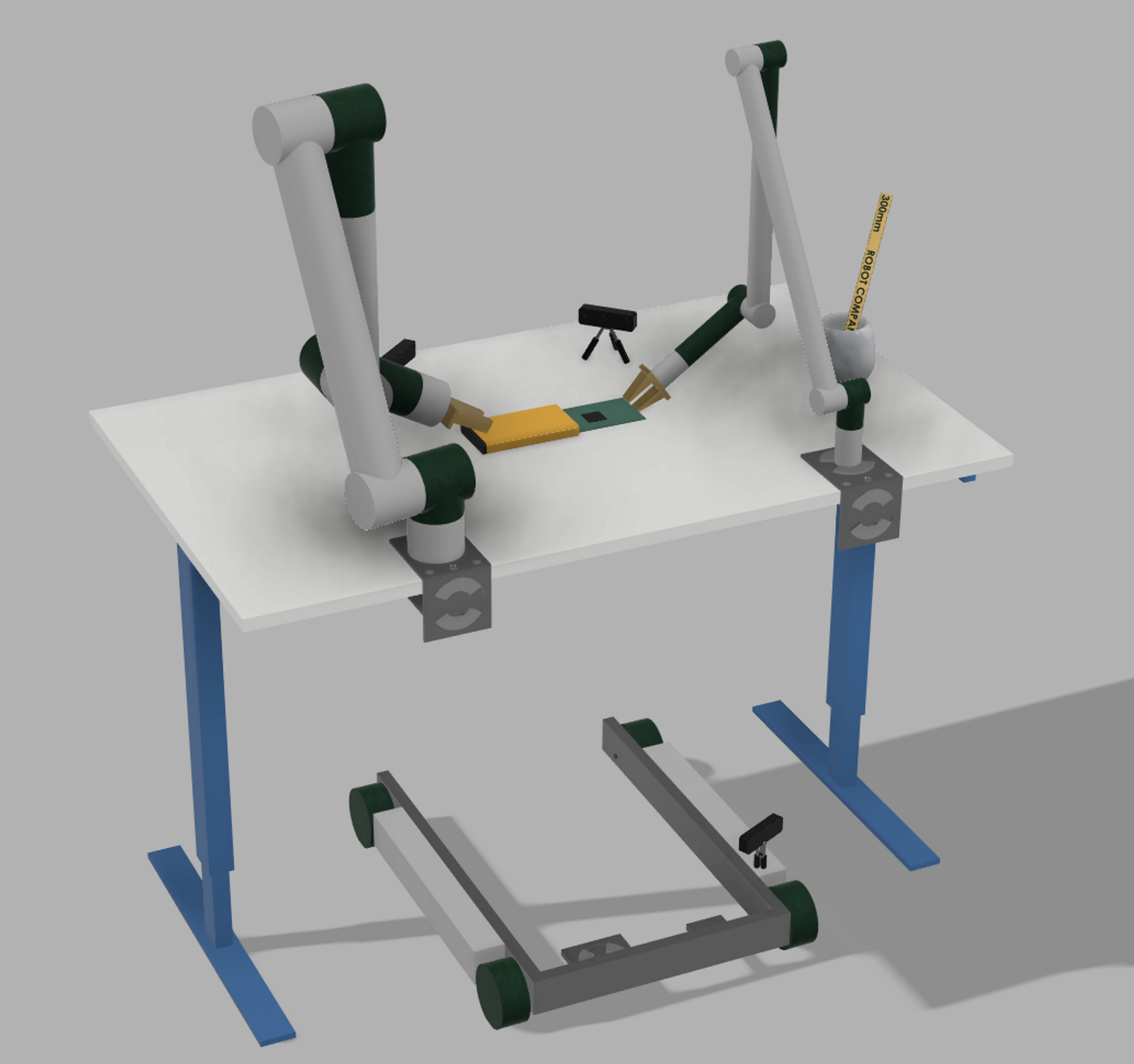
Or would it?
The idea of desk work is based on how we work today. This robot, and various others, are being designed to fit in with our working environment.
Perhaps this shows that a truly value-adding robot is not yet proven. If we had such things, then we might be adapting the working environment to cater for them, rather than ourselves.
After-all, this is why we give height-adjustable desks to our valued staff.
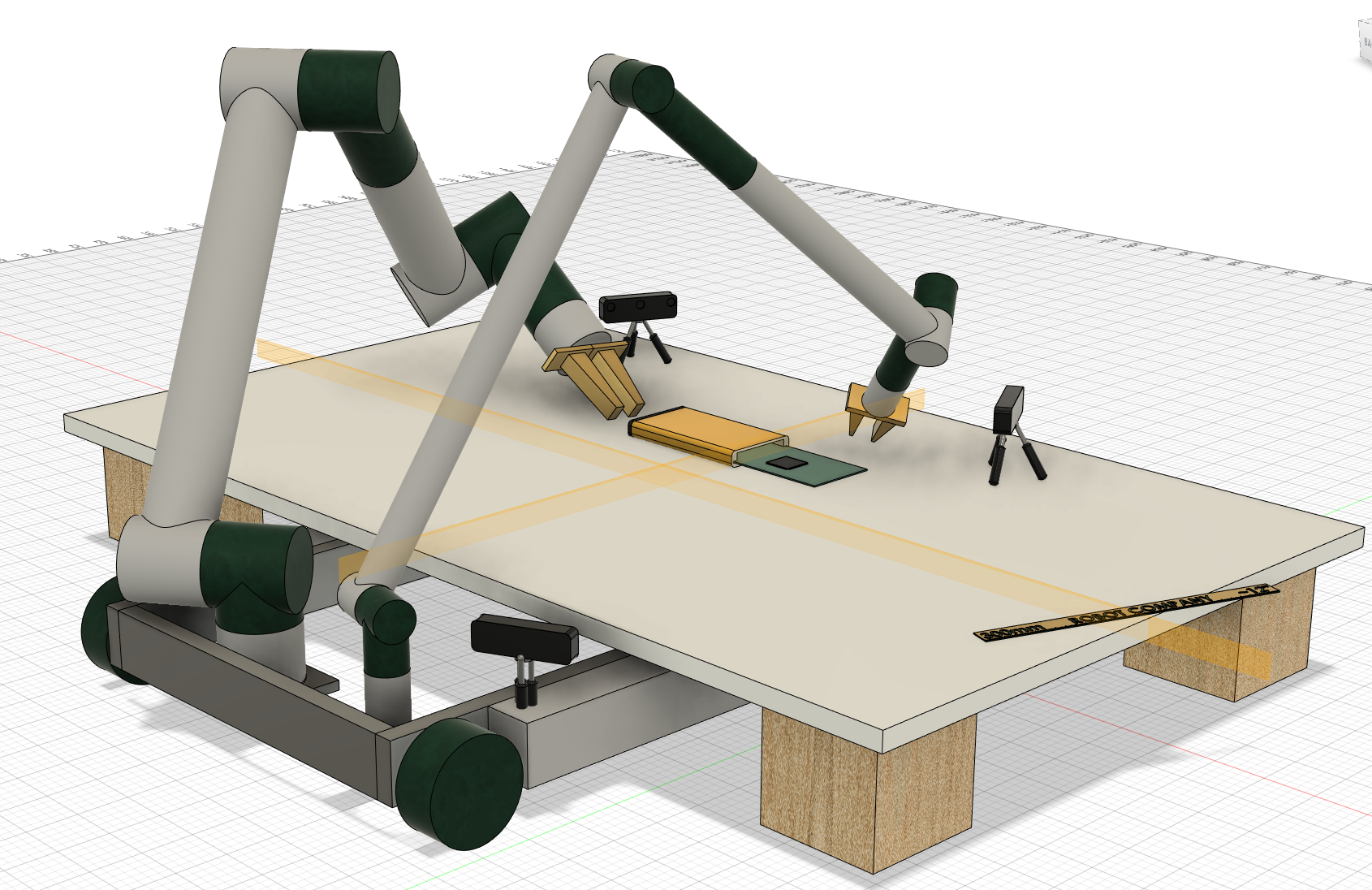
Conceptual work like this helps to get an understanding of the size and movement constraints of this design.
In the desk-top example, the working area is a short distance from the arm's base (where it mounts to the desk). In the low-desk and floor examples, the working area happens to be further away. At some point, I'll need to go over some studies on dexterity, in relation to working area and component dimensions.
This is not to mention strength of the parts. The smaller arm does look rather flimsy at the moment.
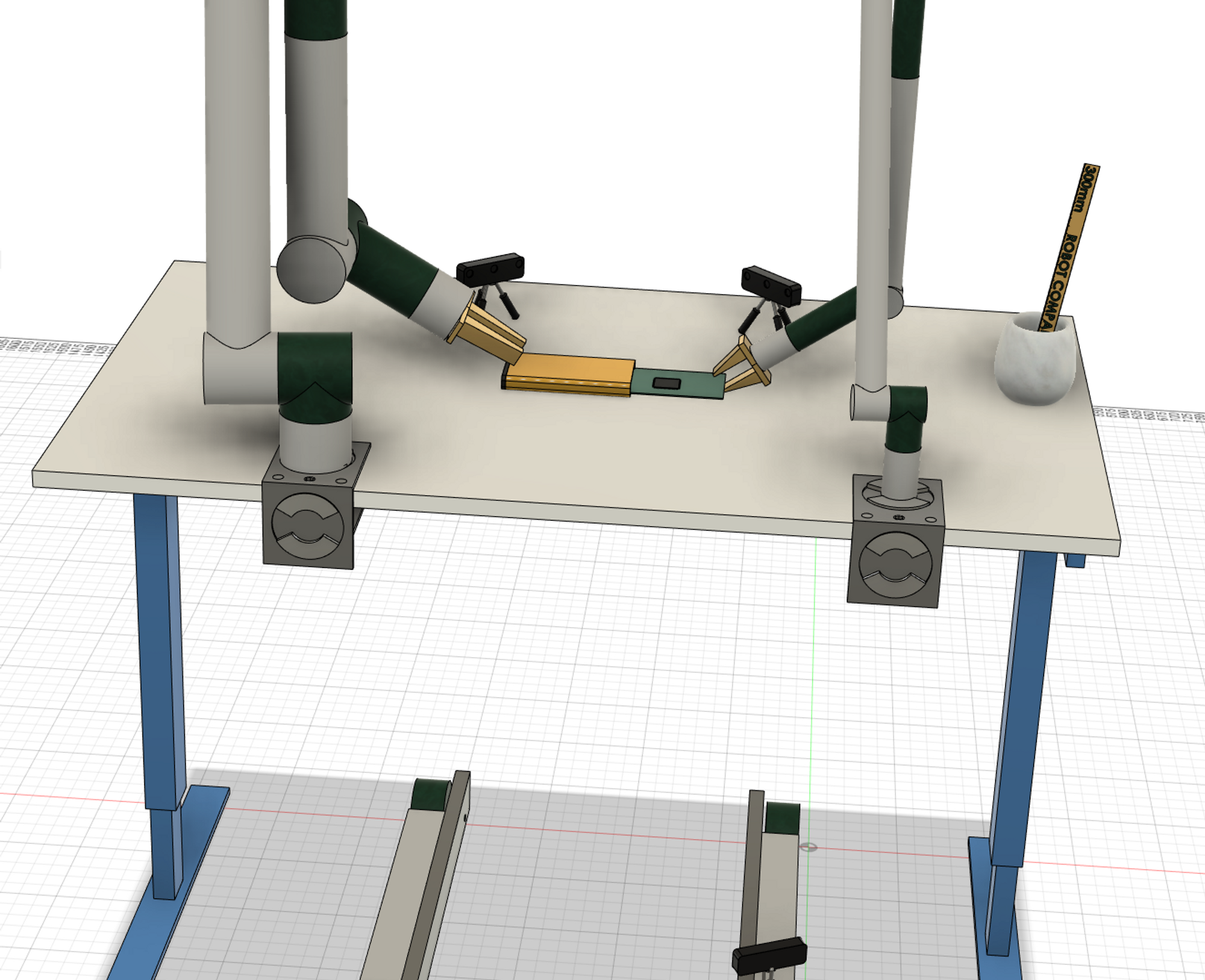
Props
Cameras
I've added some small cameras on tripods that either mount to the robot or free-stand on a surface. The idea is that these are placed by the robot in order to get a better visual angle of the work.
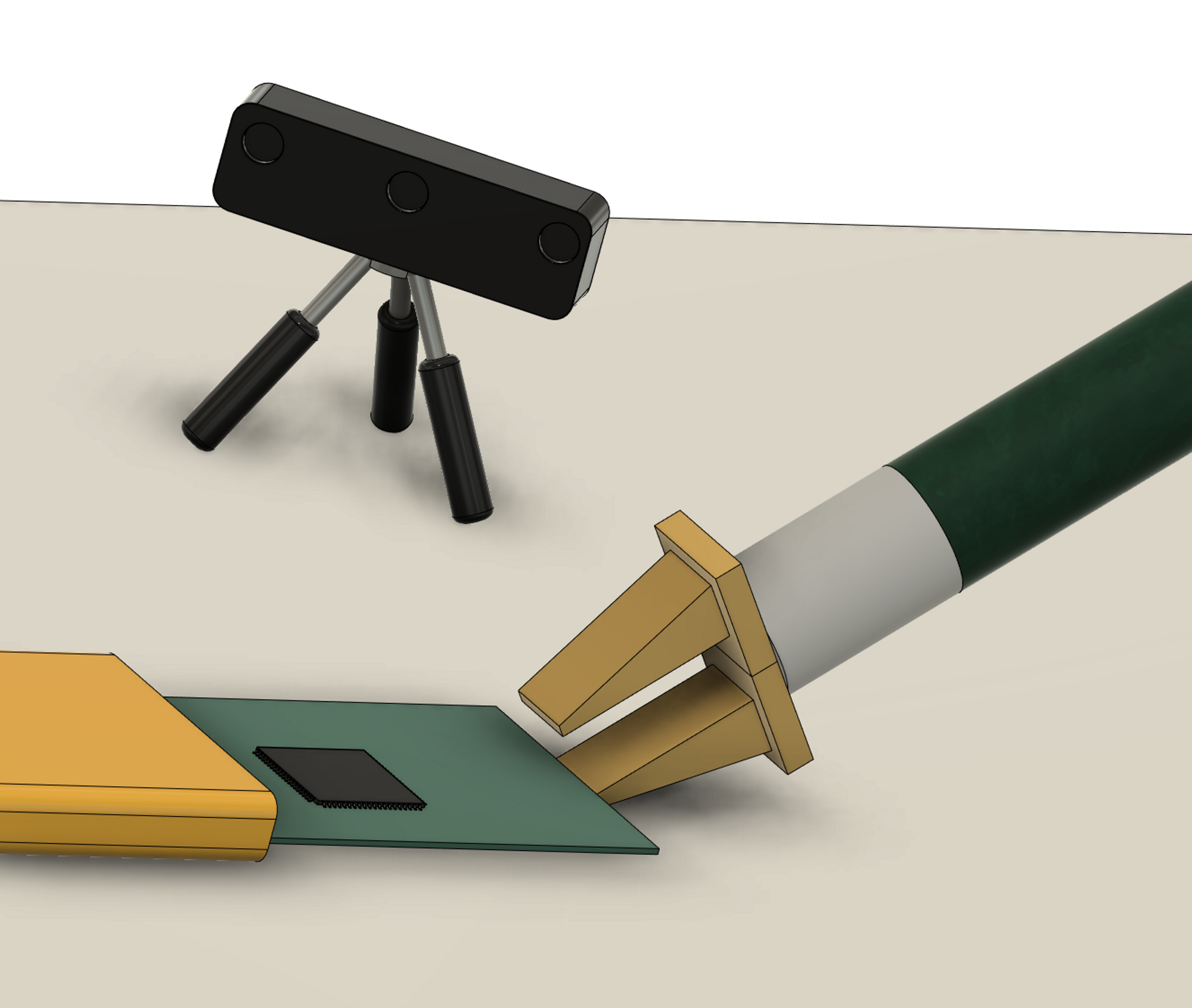
The camera is a quick mockup of the OAK-D-Lite. I stumbled on it when searching for robot depth perception. However, workshops on the visual system are quite some time away. This kind of depth perception might not even be necessary.
The little tripods are based on this tutorial. They are not based on any real product. They area fully articulate models (you can adjust the legs like a real tripod). Totally unnecessary at this point, but fun to make.
Ruler
Before adding the desk, these cameras made the robot look gigantic, so I came up with this ruler prop in order to communicate scale in every image.
Communicating scale is important (citation needed!: I'd love if someone could give me a link to a funny example misunderstanding scale.)
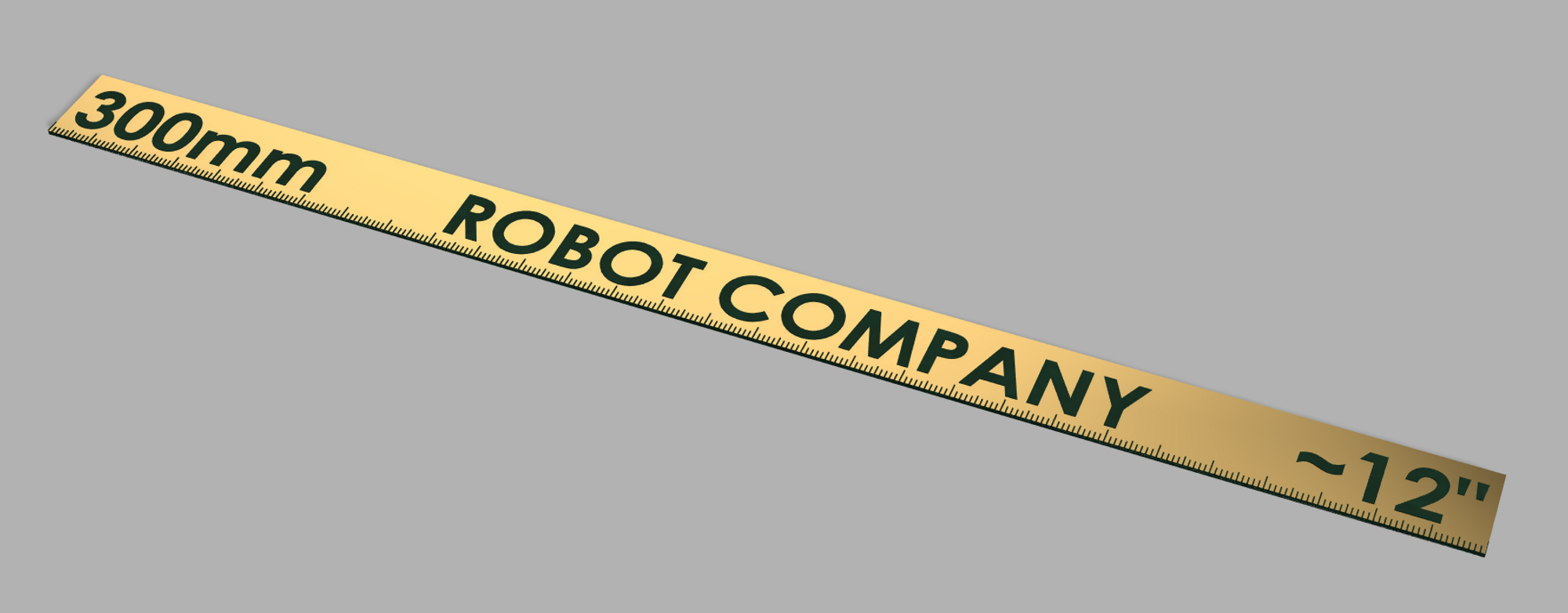
I chose a ruler based on this peer-reviewed-document. However, I speculate that it might be old data as there is no mention of using a banana.
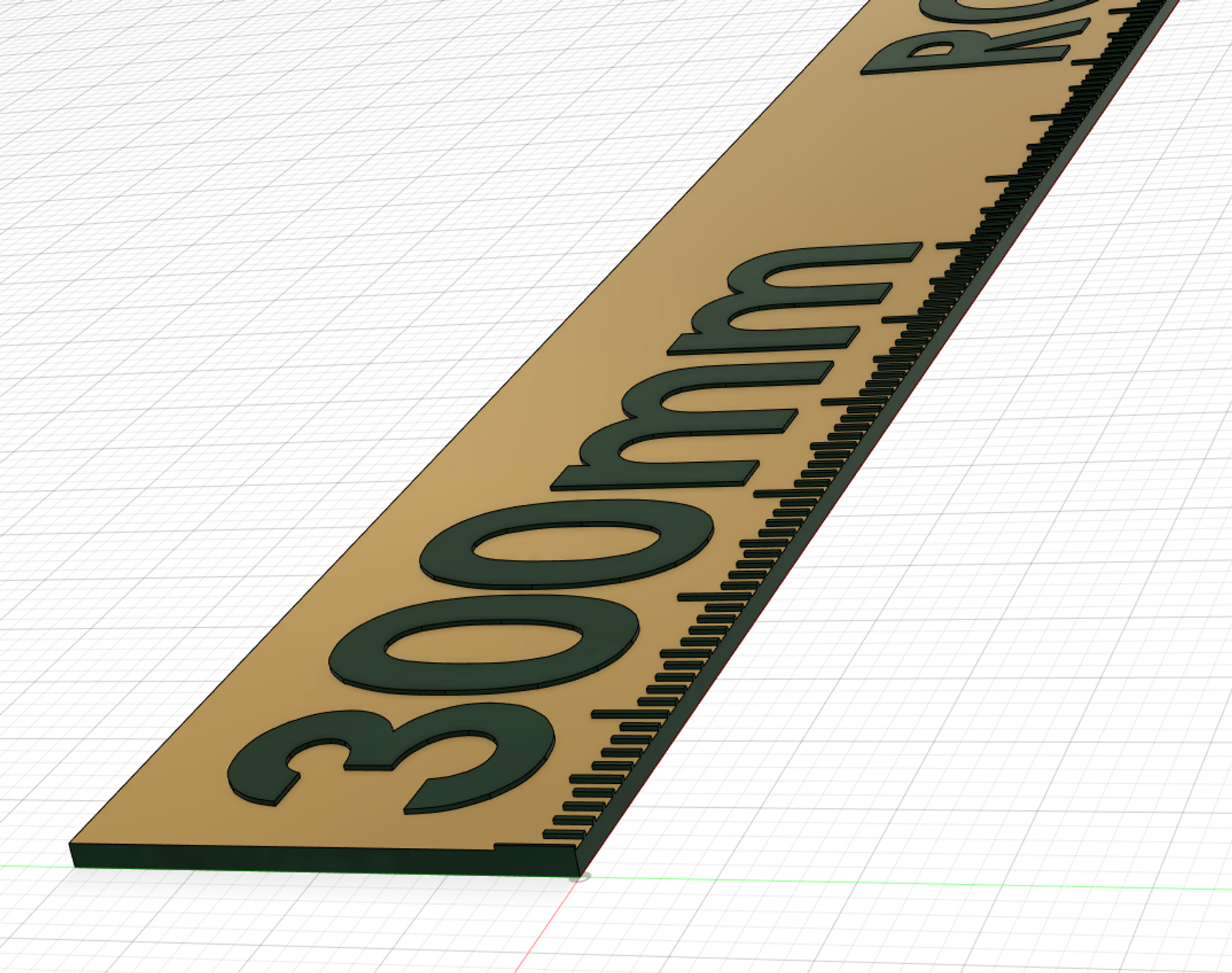
This ruler took way longer than I expected, and still probably doesn't do its job well. Would be nice to hear from people if it made any difference.
Claws
Clearly no work is done on the claws / grabbers / etc.
More on this later.
Can I get the files?
Unfortunately, when I export the files, it looks like this. This might be a deal breaker for Fusion 360. But it could also be because don't know what I'm doing
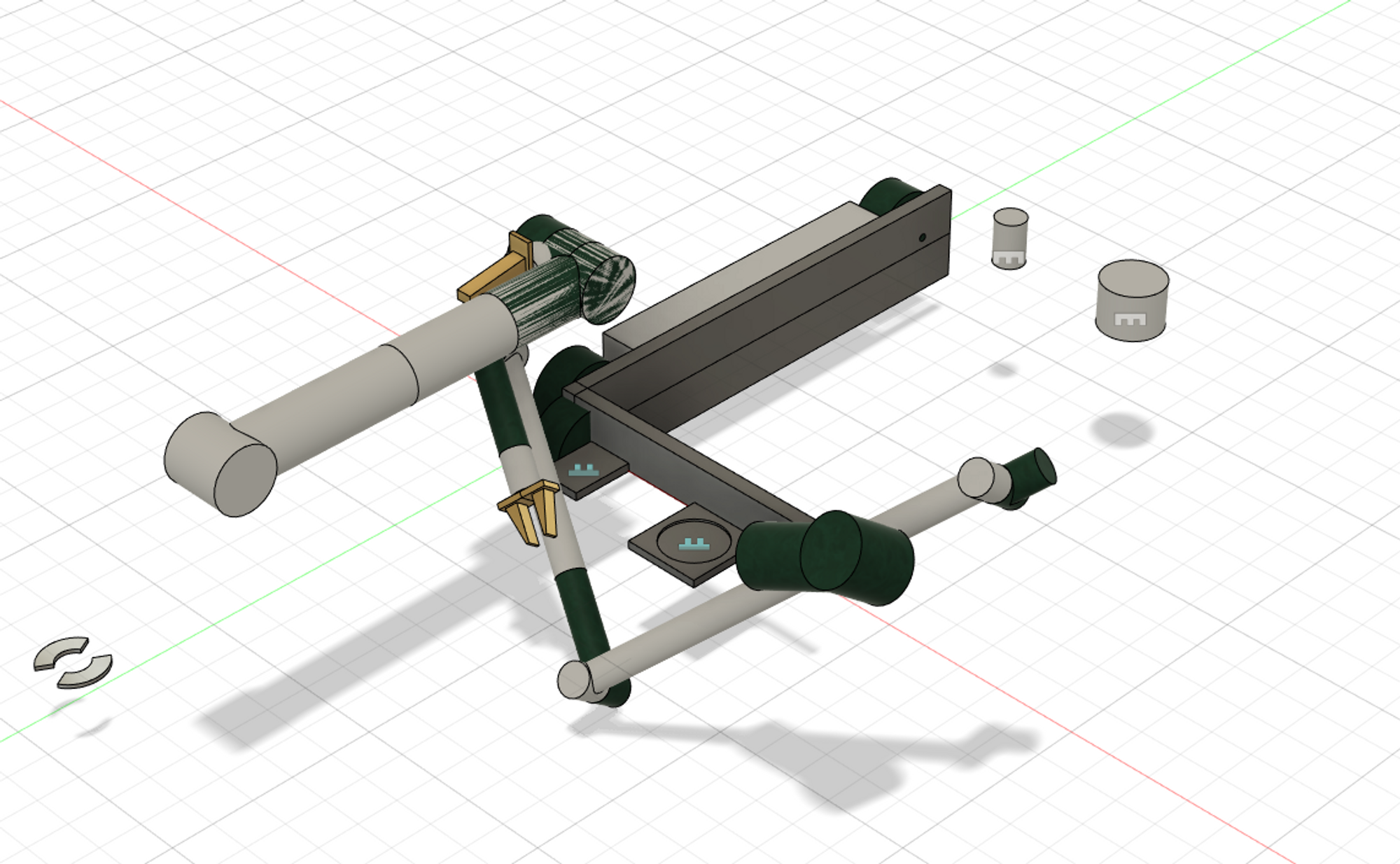